Weight Reduction In Automotive Design Manufacture. Weight Reduction through the Design and Manufacturing of Composite Half-Shafts for the EcoCAR 3.
Source Weight Reduction In Automotive Design And Manufacture Ppt Video Online Download
While weight reduction in automotive design and manufacturing has been on-going for several years in the area of powertrain technology lightweighting has been a difficult challenge to overcome due to functional requirements as well as material and manufacturing constraints.
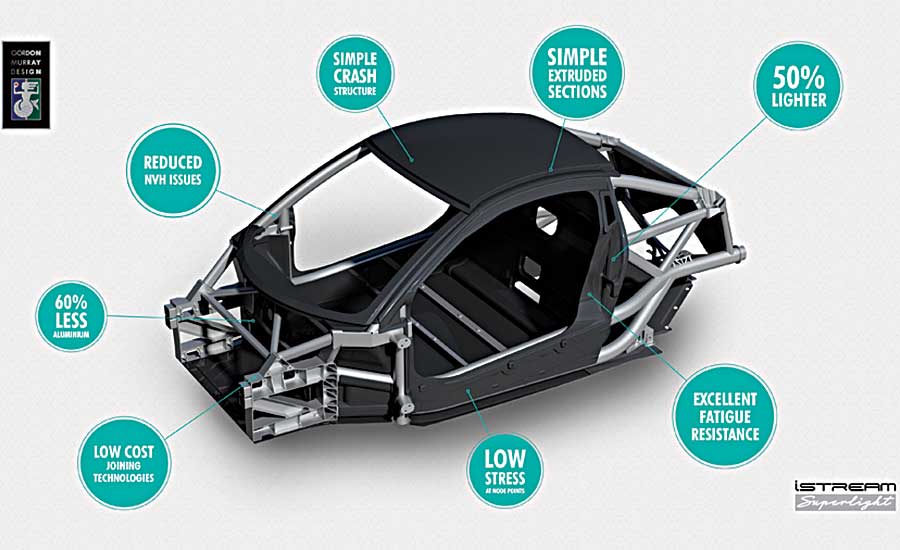
. It is a known commodity with a well-established global supply chain. Because our team often follows up on design with prototyping our approach to weight reduction is driven by fundamental theory but grounded in practice. The engineers achieved most of that reduction in the trucks frame which is made from a combination of aluminum and high-strength steel.
Magnesium parts are 33 lighter than aluminium and a whopping 75 lighter than steel. Lets explore generative design workflows that drive additive manufacturing part consolidation performance weight reduction and fluid flow. Using lightweight materials such as aluminum and carbon-fiber or optimizing existing vehicle designs are some of the key strategies adopted by manufacturers in the automotive industry.
The overall weight of the 2019 Dodge Ram 1500 pickup truck has been reduced by 225 pounds. Car Weight Reduction. The careful selection of these automotive materials enables designers to improve durability meet loadbearing requirements and achieve reduction in vehicle weight 2.
Aluminum is steels main challenger thanks to a 35-40 percent mass reduction over lower grade steels. The word lightweight is on every auto manufacturers lips lately and for good reason. A variety of weight reduction strategies are adopted by different automakers to minimize weight in automobiles.
Recycling and joining technology are also considered. Our weight reduction design approach optimizes both material and structural efficiency while delivering a cost effective manufactureable design solutions. Weight reduction in automotive design and manufacture is a priority across the industry as strict new regulations push for greater vehicle efficiency and CO2 reduction in the US Europe and Asia.
A variety of weight reduction strategies are adopted by different automakers to minimize weight in automobiles. Use of light weight materials Removing contentfeatures. Most of the main exterior panels are made from aluminium with.
Additional factors to consider before embarking on lightweighting design. The Multi Material Lightweight Vehicle MMLV developed by. Using lightweight materials such as aluminum and carbon-fiber or optimizing existing vehicle designs are some of the key strategies adopted by manufacturers in the automotive industry.
Introduction The effect of policy initiatives Weight saving methods Competition between OEMs Mass reduction and vehicle lifecycle CO2 emissions Barriers to weight reduction DifferentiationSafety Process development Cost considerations. Additional factors to consider before embarking on lightweighting design. Press-hardened parts with their extreme high.
Up to 10 cash back Weight reduction in automotive industry can be achieved by the use of advanced high-strength steels AHSS. The vehicle which launched in May just won the Altair Enlighten Award for achievements in vehicle weight savingsThe composite tunnel delivers a 40 weight reduction compared to previous. Up to 7 cash back Generative design helps designers and engineers generate hundreds of valid design outcomes that satisfy design requirements.
Therefore it is necessary to proceed with a shape optimization through the use of a simulation software which can sometimes lead to a mass reduction up to 30-40. Reducing Automotive Interior Weight With a High-End and Tech Interior. To achieve this goal university teams across North America.
The Figure below provides the data on the tensile strength and density of filled plastics polymer composites metals and alloys. The results of this change in thinking can be dramatic. Support ribs and honeycombed sections reduce part weight while retaining structural integrity especially with injection-molded thermoplastic parts.
These materials demand appropriate cutting processes. Support ribs and honeycombed sections reduce part weight while retaining structural integrity especially with injection-moulded thermoplastic parts. Suspension and engine mountings are made from aluminium either extrusions or castings.
BASF LL Products and Stellantis have been recognized for lightweighting success on the composite tunnel for the 2021 Jeep Grand Cherokee L. Weight Reduction in Automotive Design and Manufacture Weight reduction is again a priority across the industry as strict new regulations push for greater vehicle efficiencyCO2 reduction in the. Magnesium parts are 33-percent lighter than aluminum and a whopping 75-percent lighter than steel.
Weight reduction in automotive design manufacture And right here will come probably the most awaited killing manicure with long device guns all in your nailsWont you like to tease your friends and frighten your enemies with this Resourceful 3d Nail Artwork Pictures. Lightweighting or reducing the weight of a car is essential for staying competitive in an evolving market. Weight Reduction in Automotive Design and Manufacture.
CAR predicts that aluminum will increase from the current 10-13 percent to 20-22 percent of the BIW and closures subsystem. While all those weight reduction efforts are impressive most experts say theres still much more to done. Weight reduction in automotive design and manufacture is a priority across the industry as strict new regulations push for greater vehicle efficiency and CO2 reduction in the US Europe and Asia.
Weight Reduction In Automotive Design And Manufacture December 17 2013 alfredoxmwf Leave a comment This third edition report looks at policy initiatives weight saving methods competition between OEMs barriers drivers and government regulation. IHS Automotive SupplierBusiness Weight Reduction in Automotive Design and this is despite having added a wide range of safety and convenience features on the new model adding weight. From the smallest fasteners to entire vehicle architectures engineers are wringing excess weight out of new components and systems while looking for new ways to lighten existing designs.
During product design phase it is possible to detect spots whose excessive thickness could cause a superfluous increase of production costs. Engineering Solutions for Sustainability. Materials and Resources II.
EcoCAR 3 is a university based competition with the goal of hybridizing a 2016 Chevrolet Camaro to increase fuel economy decrease environmental impact and maintain user acceptability. Weight reduction is again a priority across the industry as strict new regulations push for greater vehicle efficiencyCO2 reduction in the US and Europe. Weight reduction benefits.
Use of light weight materials Removing content. This advanced computation delivers outcomes that work in the real world. Adiabatic blanking is a suitable process to process AHSS parts with excellent cutting surface quality that does not require reworking.
Examples Of Overall Vehicle Weight Reduction From Production Vehicles Download Table
Multidisciplinary Design Optimization Of Vehicle Weight Reduction Www Esteco Com
Source Weight Reduction In Automotive Design And Manufacture Ppt Video Online Download
New Design Cuts Vehicle Body Weight In Half 2018 10 22 Assembly
Weight Reduction Technologies In The Automotive Industry
Your Guide To Car Weight Reduction While Keeping Interiors High End
Automotives Body Weight Reduction
Hi Tech Aes Automotive Engineering Services Why Automotive Chassis Design For Weight Reduction Is Important
0 comments
Post a Comment